UAV Hackathon
UAV Hackathon 2023 - Safety assurance for drone autonomy
Co-organised by the Assuring Autonomy International Programme (AAIP), University of York and the Oxford Robotics Institute (ORI), University of Oxford
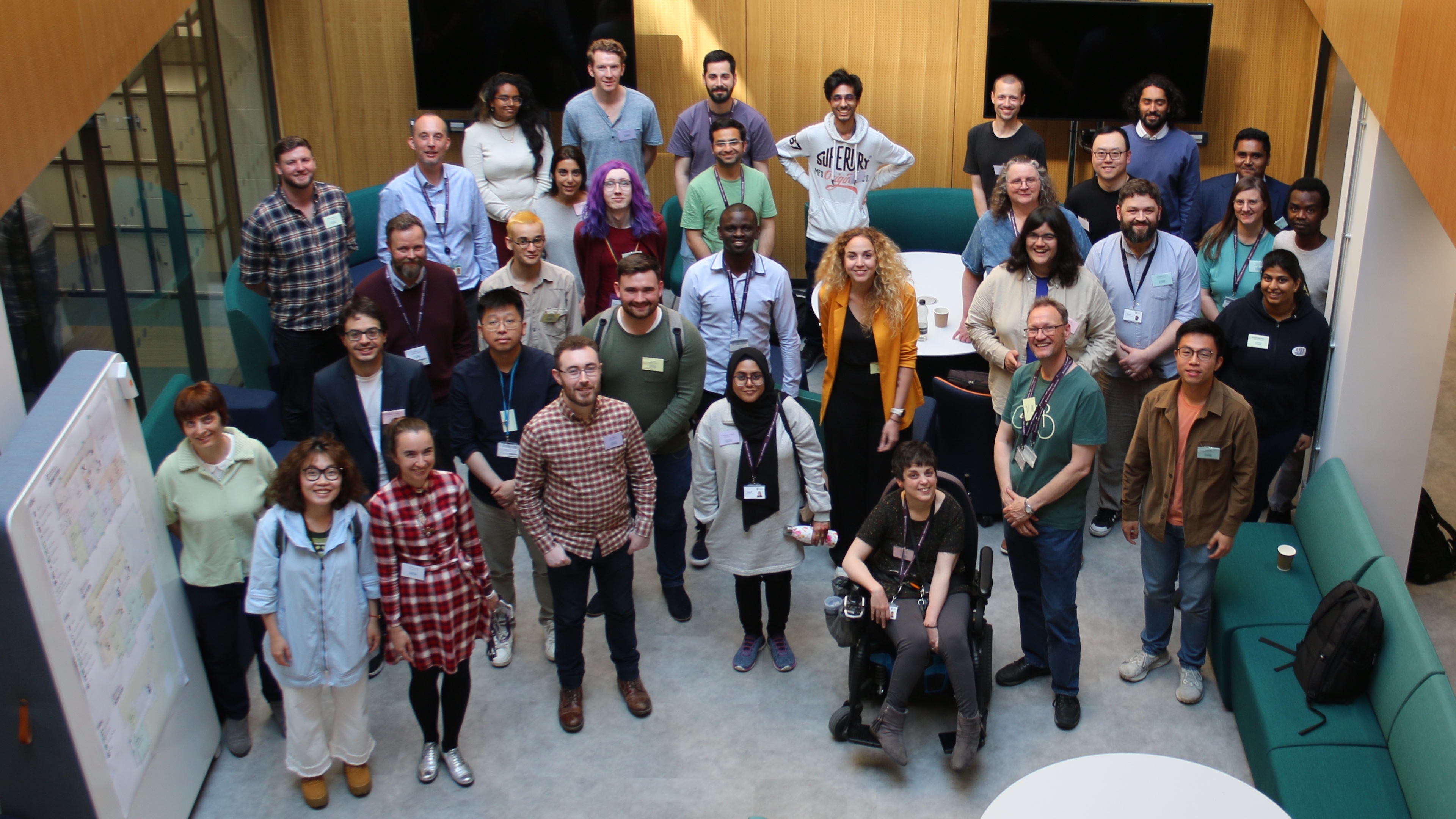
Overview
In the UAV Hackathon, participants develop a safe return-to-home function for an UAV (Uncrewed Aerial Vehicle) in a mine which is a GPS-deprived and dynamic environment. The return-to-home function will activate in the event of a failure (such as remote control loss) where the UAV must be recovered safely without human control. Teams are asked to develop the return-to-home function as well as to consider its associated safety case.
Tasks
- Technical Challenge: Develop a safe return-to-home function for a UAV in a mine which is a GPS-deprived & dynamic environment. The return-to-home function will activate in the event of a failure (eg pilot remote controller signal loss) The UAV must return & land safely without human control
- Safety Case Challenge: Develop an associated safety case
Teams
Participants were recruited from the University of York and the Oxford Robotics Institute. In total, 34 participants have worked in five teams. All teams have included members from both institutions.
Timeline
- May - Kick-off meeting @ Institute for Safe Autonomy, York
- July - Check-in (I)
- August - Check-in (II)
- November
- MINAR XI - Participants visit the MINAR XI event at the Boulby Underground Laboratory and conduct real-world experiments
- Final demonstration @ Institute for Safe Autonomy, York
Winners
coming soon ...
Related Publications
- Cannizzaro, R., Howard, R., Lewinska, P., & Kunze, L. (2023). Towards Probabilistic Causal Discovery, Inference & Explanations for Autonomous Drones in Mine Surveying Tasks. arXiv preprint arXiv:2308.10047.
Organisation
The UAV Hackathon 2023 has been co-organised as part the ASUMI project of the Assuring Autonomy International Programme (AAIP) and Lars Kunze's AAIP Programme Fellowship.
Background
Data sets
This section describes the data sets that are provided to the Hackathon participants. Participants can use one or both of these data sets to perform experiments and simulations. Participants may choose which elements of each data set they wish to use in simulations (e.g., flight path, camera data, LIDAR data) to evaluate their proposed approach, in addition to the provided environment mesh model.
Potash mine, real-life data set
This data set has been gathered by a UAV (ELIOS 3) at a salt/potash mine in the active excavation front. It shows how the UAV is being currently used in the mine (for inventory of freshly excavated front for measurement of the excavated material volume).
The flight data combines line of sight (LOS) and camera view, aided by the SLAM registered mobile LIDAR point cloud (of estimated accuracy of 0.5-2m). The max dimensions of the excavation are 8x5m (width x height). There are survey marks on the roof of some parts of the mine that could be used for navigation. This data set shows the real environment and elements that need to be avoided while flying (hanging bolts, net/cable, uneven floor). It also shows the difficulties with flying (such as moving around obstacles, dust, and wind speed ). This data set consists of all sensor information provided by the Elios 3 drone (including the initial coarse registration and full registration of a point cloud, camera footage, recorded flight path, IR data etc.)
This data set will be aided by 3D modelled obstacles that could be randomly added during the simulation.
Simulated data set
This dataset was obtained from an enclosed obstacle course has been built in the ISA lab Test Space 1. It was obtained using a PX4-based UAV, this drone has no LIDAR but can be programmed so it is suitable for experiments without a LIDAR. The obstacle course simulates mine conditions as closely as possible. However, it will is scaled down in size. This data set consists of all of the sensor data from the drone and a LIDAR point cloud obtained via TLS (terrestrial laser scanner). Obstacles have been placed on the obstacle course on the roof, and walls. There are also a set of obstacles on the floor (ground) that will simulate changing conditions on the floor that might occur. There are also survey markers mounted to the roof of the obstacle course that are representative of those found in the mine.
Mining conditions
Excavation at the front of the mine
Currently the biggest concern for the surveyors in the salt/potash mine is periodical inventory of excavated material. This is done in 2 stages, the empty space (left by the excavation) is being measured underground and then the material hauled to the surface is being surveyed again. The two surveys provide volume information that is being compared.
The underground excavation is being performed as follows. The mine is excavating mostly parallel sedimentary-type deposits. The preparation works consist of excavating long 8x5m tunnels supported by bolts (continuous miner method) and lining in the roof. Salt is mostly soft and considered as elastic rock so this is enough support for temporary workings.
The next step of the excavation is the blow out works. They start at the far end of the preparation excavation (tunnel). A short front (length of 10-15m) placed at an angle of around 120 deg is being exploded at each side. Also the floor of both the main tunnel and the blasted part is being retrieved (excavated) to the depth of up to a few metres. This makes the floor uneven since the blasting of the floor is being done on a ‘what can be done’ basis. There are 2 to 8 of those blasts done each day.
The threat to the survey crew caused by the type of the excavation
After each of the smaller caverns are blasted out there is no roof support in them also the support in the main preparation excavation (tunnel) has been damaged. This means it is no longer considered safe for anyone to be in this area of the mine. All of the surveys have to be done in the way that allows the survey crew to be just outside the excavation area. So this is the starting point for the drones.
2.1. Roof collapsing danger
There is a threat of so-called ‘roof falling/collapse’ (the situation when the geological layers of the roof are different to those above and not bonded strongly, that might cause large parts of the roof to collapse), but this is mostly taken care of by rock-mechanics calculations and geological prospecting. However, it needs to be kept in mind that this can happen. Also it might just make the roof subside by a small fraction and short, and move the bolts down. Both the roof and the potentially sticking out bolts need to be avoided by the drone.
2.2. Left elements of infrastructure
Obstacle avoidance during the flight is needed to avoid hitting bolts and metal net lining that could be low hanging in the main tunnel and other elements. There might be other elements of mining infrastructure present in the excavated part of the mine. These are usually parts of the ventilation infrastructure (rubber pipes of various diameter but normally not exceeding 30 cm), elements of electrical infrastructure (wires left, not connected to main line), testing tubes (smaller pipes for testing for methane) and strings, tapes, elements of wood and metal, and sometimes machines.
2.3. Geological obstacles
After blasting, the tunnels are uneven and have only approximate dimensions. The floor on the side tunnels is much lower than in the main tunnel. The main preparation tunnel floor is uneven since the waste rock is being stored in small piles. Also, there might be unexpected rock movement during the flight, coming loose from the roof and the sides.
2.4. Environmental concerns
The mine is located in a salt deposit that is partly infused with highly-explosive methane; the temperature underground is above 30C. The length of the excavations, and the distance of the used part of the mine from the shaft enforce strong draft ventilation. This all creates a set of environmental difficulties:
- High temperature - might affect the performance of the batteries and sensors
- Dust in the air - the tiny particles of salt dust are sticky and could glue the propellers (slowing them down as the survey progresses)
- Dust in the air - covers the sensors and limits their use (might cause the drone’s pre-arm safety checks to fail, preventing take-off)
- Dust in the air - limits the portion of the flight in which the drone is visible to the pilot thus the flight with camera view is necessary. However the camera footage is also obscured by the dust (additionally the camera view does not cover the full 360-degree view and might be not enough to go around thin (bolts) obstacles hanging from above. Note that we will keep the drone within LOS while under pilot control, and thus we will not consider flight paths outside LOS for the experimentation while under pilot control (however, the drone may operate autonomously outside of LOS during the automated/autonomous return phase).
- Ventilation of the excavations - in current scenarios the main ventilation is turned off for the flight, however some residual draft might be present or appear at random if conditions change (e.g., someone opening the air dam near the flight area)
- Methane - the mine has some growing methane concerns, this is being addressed with only being allowed to fly if the methane concentration is below a certain number. Existence of methane limits the construction material that the drone can be made of. Also the methane concentration is driven by how much ventilated pumped air is diluting the methane, thus when the ventilation is turned off for the flight this concentration might rise up quickly.
2.5. GPS deprived environment and communication concerns
An underground mine is a GNSS deprived area, thus there needs to be another way of navigating without dependence on GNSS.
When the UAV turns round a corner in the mine tunnels, the communication module loses contact with the pilot’s controller. This also might happen if the UAV flies beyond the maximum communications range of the controller.
2.6 Return to home landing point
The place where the UAV starts from is usually just in front of the out of access zone. The natural return to home place would be to get back there. However if the draught is too strong or other events change the geometry of the environment, there might be an issue with trying to get to the same place. The part of the mine that is being prepared to be excavated is populated by people, heavy machinery, and infrastructure (including electric). So there is a real chance that the UAV flying on autopilot might hit one of those objects and cause serious damage to itself or the surroundings and people. Thus various scenarios for return to home are needed. The assumed amount of information known beforehand by the UAV for mission planning purposes will need to be discussed, including what considerations will need to be made by the UAV when assessing candidate landing locations.